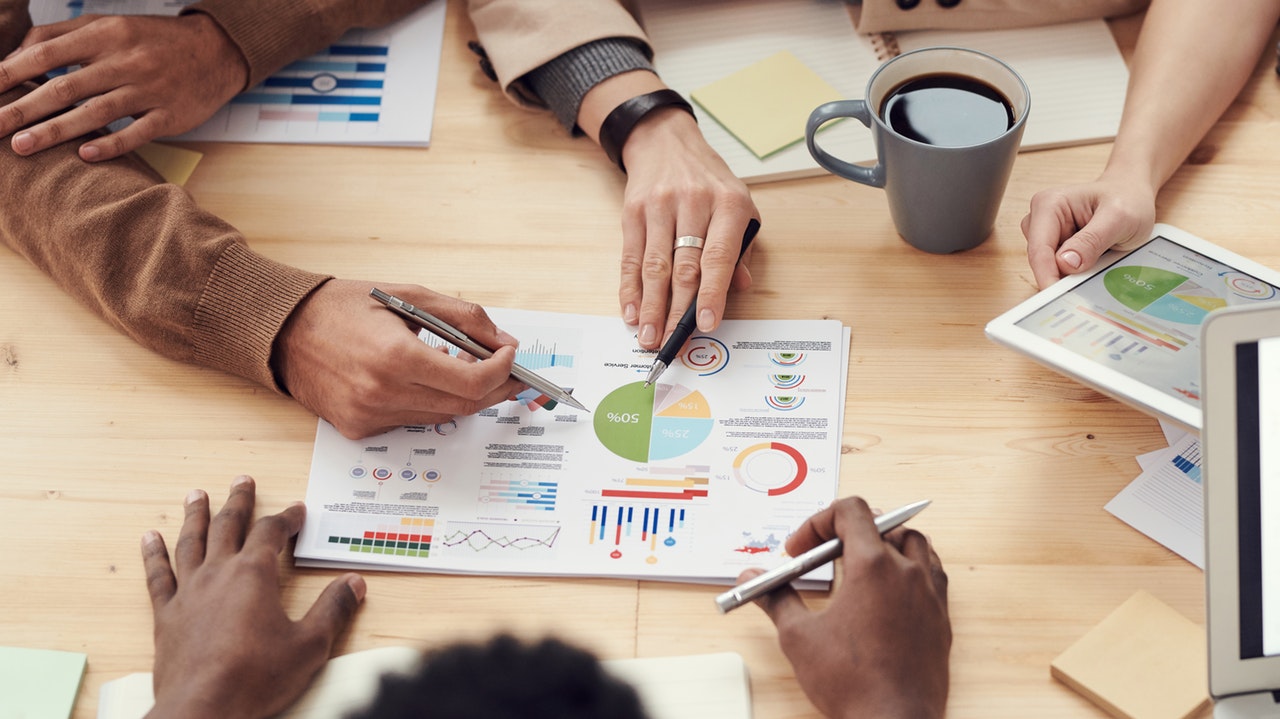
It’s a situation we often see... a Sensory QC Program is in the organizational spotlight because of either shifting priorities, a recent uncaught issue, or the perception that they are slowing down production. Whatever the reason, it’s a clear sign that a program is mis-aligned and in need of adjustment. Here are a couple of tips to help you generate better data, save money, and stay true to the mission of your program.
Tip #1: Collect Data That Has Value
How do you know what has value? A Sensory QC Program’s job is to provide stakeholders the information they need to make good decisions. So, if you can’t easily identify who benefits from the results of a test, you don’t need to be doing it.
The tests that really matter are the ones that have clear results and clear communication plans associated with them. It’s tempting to want to collect more data than you need for advanced analysis, trending, or future projects, but panelist time and attention is limited. Focus on what you need first, and then build from there.
Tip #2: Flag Issues First, THEN Troubleshoot
Imagine calling a mechanic to inspect your car every single time you leave the house. Of course they could fix your car on the spot if something is wrong, but at the expense of the extra labor and being late everywhere you go? Instead, most drivers check for problems on their own and then go to the mechanic when something is wrong.
The same thing applies to Sensory QC, don’t troubleshoot a problem until you know one exists. Run tests that flag problems early and often, and have a follow-up plan to collect troubleshooting data. Why collect all of that troubleshooting data upfront if it won’t be used?
Tip #3: Solve for Time
The most precious resource for any Sensory QC Program is time, and the best programs take this into account early and often. Tasks like panel execution and data analysis can be bottlenecks because of the time and expertise required, but they can also be automated with the right QC process in place. Time spent evaluating samples can also add up fast, and long evaluations can cause people to lose interest and give less accurate data. Trimming down the amount of time each panelist spends has a multiplying effect, and there are many cost-effective tools available to make data entry painless, so take advantage!
DraughtLab offers practical and approachable Sensory Analysis Solutions that deliver real-world value to food and beverage companies. Visit our website or reach out to us at info@draughtlab.com to learn more!